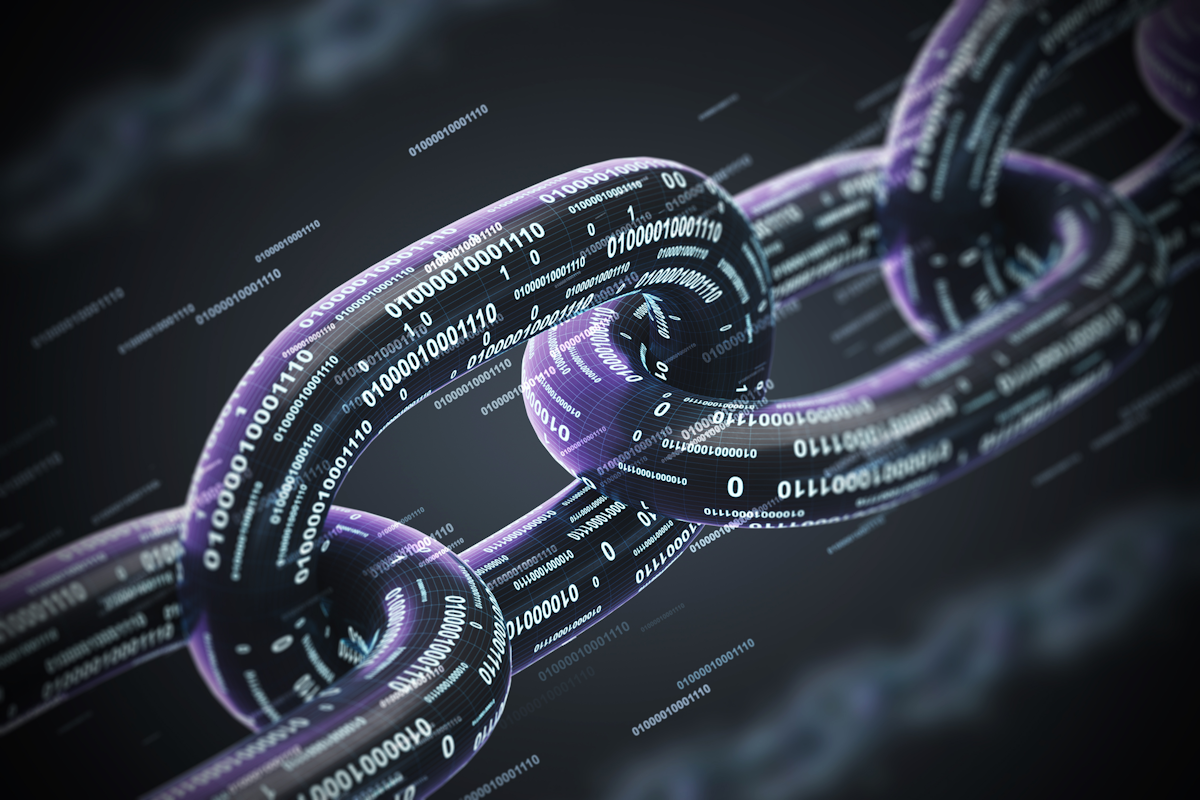
Most manufacturers have yet to embrace maintenance, reliability and asset management as core drivers of their digital transformation strategy. We all know that machines are critical and that we need to address issues before they cause a catastrophe. But, that work requires significant manual resources and still results in frequent downtime, production loss and supply chain disruptions.
One 2017 survey of 600 IT and field service decision makers found 82% had suffered one or more unplanned outages in the previous three years. The impacts of unplanned downtime are expensive and varied, but the most common consequence is the inability to deliver products or services, which translates directly into lost revenue.
Currently, most industrial companies don’t continuously monitor the health and performance of machines. Instead, they rely on archaic failure models based on machine usage. It’s challenging to predict industrial failures using operating hours or life cycles, and as the survey shows, this outdated model simply doesn’t work to prevent operational disruptions.
With these results, it’s hard to imagine maintenance and reliability becoming key drivers of innovation and excellence. Enter machine health, which uses Internet of Things (IoT) and artificial intelligence (AI) to predict and prevent machine failures and improve machine performance. Manufacturers using machine health are seeing dramatic improvements that can accelerate wider digital transformation across the supply chain.
A global CPG company has saved millions of dollars by preemptively diagnosing machine problems and prioritizing the machines most critical to operations. Improvements have been so significant that the company is creating new roles specifically focused on machine health and using performance data to inform daily meetings. It’s even using machine health insights to improve quality control and supply chain stability. This top-down transformation is possible at any facility that takes machine health seriously.
The journey to machine health
Machine health is insight-based, while traditional approaches to reliability, maintenance and operations are compliance-based. This means it’s inherently predictive and prescriptive, while traditional approaches are reactive or preventive. A machine health solution allows companies to switch from these older approaches to one that can sense precisely when machines will experience a reduction of performance, prescribe corrective actions and operational adjustments to avoid it, and schedule necessary maintenance.
Performing maintenance, reliability and operational activity based on the machine’s real-time condition (rather than less reliable indicators like age) eliminates unplanned downtime and a significant portion of the reactive and preventive workload. Machine health also minimizes downtime caused by maintenance itself because machines only receive service when absolutely necessary.
The people who design, maintain, operate and manage industrial assets now have access to the same machine health data in real time, which leads to enhanced collaboration and frees up resources for high-value work. Instead of performing unnecessary routine or reactive activities, maintenance and reliability professionals can focus on unlocking production capacity, uptime optimization and process improvement.
Machine health is also about understanding the relationship between individual machines and overall performance. Prescriptive mechanical health diagnostics and operational performance analytics reveal how each part of an operation fits into the whole. Those insights have a transformational impact on manufacturing operations and help improve outcomes across the board.
As part of a larger asset management strategy, machine health improves uptime, manufacturing capacity, productivity, product quality, time to market, supply chain-level agility, risk reduction and predictability of production. Simultaneously, it promises dramatic reductions in maintenance costs, labor costs, and inventory holding.
What makes machine health effective
AI-driven machine health solutions consist of four key components that work together to transform industrial operations.
1. Monitor
Sensors continuously capture streams of high-quality, standardized mechanical and operational data from machines. Vibration and magnetic data are sufficient to detect most mechanical and electrical faults in rotating equipment. Other sensor data — like temperature, ultrasound, fluid analysis, pressure, and electrical current — can help augment this coverage and enable diagnostics of additional components.
Sensor data can be supplemented with operational data streams (like machine speed, load and recipe) to enable even more precise predictions and recommendations for operational performance across individual machines, machine centers and production lines.
Without continuous and standardized data, machine health diagnostics and performance analytics become sporadic and ineffective; they simply won’t scale across machine types, facilities and operational use cases.
2. Diagnose
Deploying the right sensors isn’t enough. AI insights should enable the practitioner to easily understand what the potential issue is, which parts of the machine or the production process are affected, why the issue is emerging, how to improve the condition with the right corrective or preventive actions and when they should act.
Cloud-based AI algorithms can use mechanical and operational data to not only predict the condition of the machine, but also help optimize the performance of other machines and systems around it. For example, an emerging mechanical issue on a critical component of a production line can impact product quality downstream. By using machine health and performance insights across the entire production line, manufacturers can quickly link mechanical issues to production outcomes, prescribe an early intervention, and improve the design of the overall process.
3. Guide
Machine health guides reliability, maintenance and operations teams on what to improve, how and in what order. Reliability teams use AI-driven insights to identify and eliminate the root causes of failures and replicate these best practices across the organization.
In addition, machine health provides the ability to look into the future — by making accurate predictions of asset life span and performance based on its real-time condition. This level of insight enables more predictive and dynamic asset strategy and operational planning. Asset performance can now be directly tied to expected production outcomes and supply chain strategy and the organization’s overall financial needs.
4. Act
Machine health insights enable maintenance and operations teams to plan activity based on a common set of machine metrics and real-time insights. Technicians and operators can act on recommendations based on the actual condition of the machine and root cause diagnostics. Together, these teams can collaborate to eliminate emerging issues and optimize production processes and control parameters. Machine health solutions also make it easier to capture institutional knowledge; provide expertise remotely; and standardize best practices for reliability, maintenance and operations.
The industrial world is undergoing a rapid shift toward digitization that’s been significantly accelerated by the Coronavirus disease (COVID-19) pandemic. Machine health provides a proven, critical use case and serves as a foundational part of this shift. This is why manufacturing leaders are embracing a new era of machine health and performance.
"machine" - Google News
February 07, 2021 at 04:54AM
https://ift.tt/3ryMQLJ
A New Era of Machine Health, Reliability and Performance - Supply and Demand Chain Executive
"machine" - Google News
https://ift.tt/2VUJ7uS
https://ift.tt/2SvsFPt
Bagikan Berita Ini
0 Response to "A New Era of Machine Health, Reliability and Performance - Supply and Demand Chain Executive"
Post a Comment